The project was with the MIT Digital Structures research group as part of an ongoing project to create concrete beams without rebar. Steel rebar has a large carbon footprint and can be difficult to obtain in developing countries with increased creation of infrastructure. This project seeks to design fabric formwork for concrete beams to replace rebar, promote sustainable material consumption, and improve building performance. In particular, my role was to develop a fast way to visualize the final form of the knitted formwork after pouring concrete, to help optimize the formwork for beam performance during initial design.
Digital Structures, MIT: Nicole Teichner, Mohamed Ismail, Lavender Tessmer, Caitlin Mueller
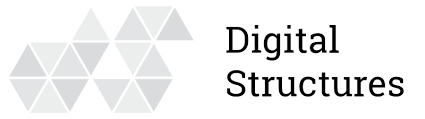
This project was computational, with use of Grasshopper, Rhino, and Python. Two scripts were produced from this project. The first script determines shape of the fabric formwork after being knitted. The second script determines the form after concrete is applied, taking into account both hydrostatic and gravitational force.
Fabric formwork is knitted in an industrial knitting machine. The formwork consists of an external shell which holds the concrete, and attached "fins" to provide internal support and hold the sides of the external shell. Refer to the image below of the general form of the formwork and how the formwork is knitted in the machine.
Profile of a rigid shell w/o fins
7 fins contained in the shell
4 fins contained in the shell
The fabric formwork is knitted vertically to become the shape on the right before concrete is poured. While being knitted, fins cannot overlap, but fins can have holes in it and/or be knitted upside-down.
The photos below demonstrate the performance of the first script in the grasshopper/rhino interface. An initial profile is created to represent the desirable form of the formwork (shown in black). The results of the script are shown in red, and reveal what the actual form will look like once it is removed from the knitting machine and opened at varying distances. How far the formwork can open will be dependent on the length of the fins. This script can also be used to determine if the fins will overlap while being knit and the design is therefore not feasible.
The images below depict a variety of final formwork profiles before and after concrete is applied. The formwork can be held at a variety of anchor points to maintain its shape while pouring. However, it is most ideal for form to be determined by the maximum length of the fins as opposed to location of anchor points. The less deformation, the better. The post-deformation forms can be combined with scripts for beam optimization, to determine which forms will lead to the beam with the least amount of material and the strongest performance.